As we know that there are various fields available in business central related to production which are available on the “Replenishment Tab”. We also have fields on “Planning Tab” that are used by the people in production, but these are only planning parameters.
In this blog we will discuss briefly about these
Step 1: - Search “items” in business central

Step 2: - Item list will open.
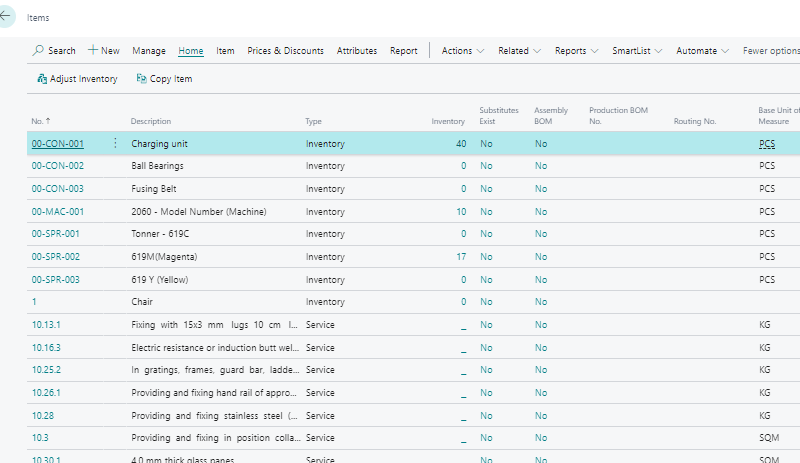
Step 3: - We will select an item which we want to create Production order functionality. We define various parameters on item card.
-
We first go to “Replenishment Tab” and Select “Replenishment system” as “Prod. Order”.
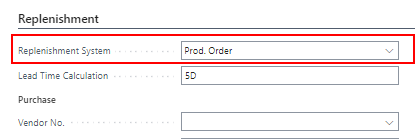
-
Then we define the Manufacturing Policy, here we have two options to select “make to order” and “make to stock”.
Make to Stock – This policy is used when we want to reproduce the item and put in stock.
Make to Order – We can make Production order directly combined with sales order, in the sales order by this functionality, when we use this functionality, we can have more than one production order line on each production order.
Normally we can see that we have only one production order line per order on production order to produce.
Routing: - which defines the way we persist the item with the operations or the work centres, machine centres. For this we go to specific setup.
Production Bom: - Here we define all the raw material or components we need to produce this finish good. For this we go to specific set up where we define all items, quantity per etc.
Make a note that we can use one Production order or Routing on more than items.
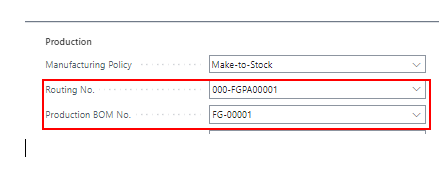
Rounding Precision: - it basically helps to reduce the rounding issues in future when we use alternate units of measure, the value in the Qty per unit of measure field help calculate the quantity in base unit of measure, which can lead to rounding issues.

Flushing method: - It defines how the items will be flushed for the production order like if we have selected flushing method as Forward then the consumption of the component will take place at the time of refreshing the order or changing the order status from the firm planned order to Released production order. When flushing method is Manual then the components will be flushed/consumed when we flush it from consumption journal. If we choose flushing method as Backward, then flushing will happen when we finish the order.

Overhead Rate: - It is the additional fixed cost which we can add to item to add on the standard cost. It is basically used to cover all the indirect costs on the production area, like maintenance cost of the machine.

Scrap Percentage: - Here we set up the Scrap percent it affects the calculation of the standard cost, and it will make the consumption amount on the production order be higher if we have a fixed scrap percentage on the item card.

Lot Size: - it displays the normal quantity we produce this item in and its relevant for calculating the standard cost price as the set up time on the production order or the set up time on the routing will be split into lot size amount, when calculating the standard cost.
